The completely new ROTIN® 3
After bringing the Rotin 2 (the current version) to market, we have now been working for more than 1 year to bring an even more efficient and of course patented version to market, the Rotin 3!
So now we proudly present the Rotin 3, a completely new design from the ground up!
After many prototypes and evaluations, we were able to reduce the coefficient of friction in the new design, which greatly improved the Rotin 3’s rotation.
The throughput of the blasting medium has been increased by more than 100%, allowing the glass beads to achieve exceptionally better flow and spin.
With this new and patented design, when in use, it is simple to see that the Rotin 3 is actually rotating. This allows the operator to know while treating his workpieces that the quality of the treatment is guaranteed, stain free and food grade!
Currently, the first batch of new Rotin 3 is being produced and we will be phasing it out before going fully international.
Distribution will mainly be in the hands of our partner Airblast. Airblast is an international acting company that pre-treats the surface properly with the necessary equipment.
Airblast is currently putting together a handy Rotin blasting unit that will allow the Rotin 3 to maximize its potential. This combination will ensure that the operator is fully capable of delivering the intended high quality, every time.
Translated with DeepL.com (free version)
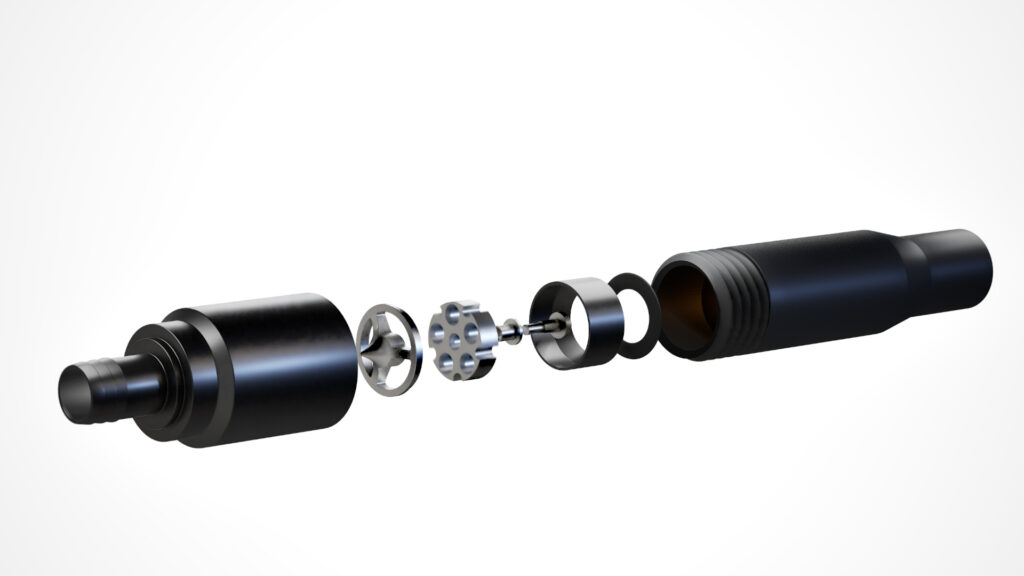
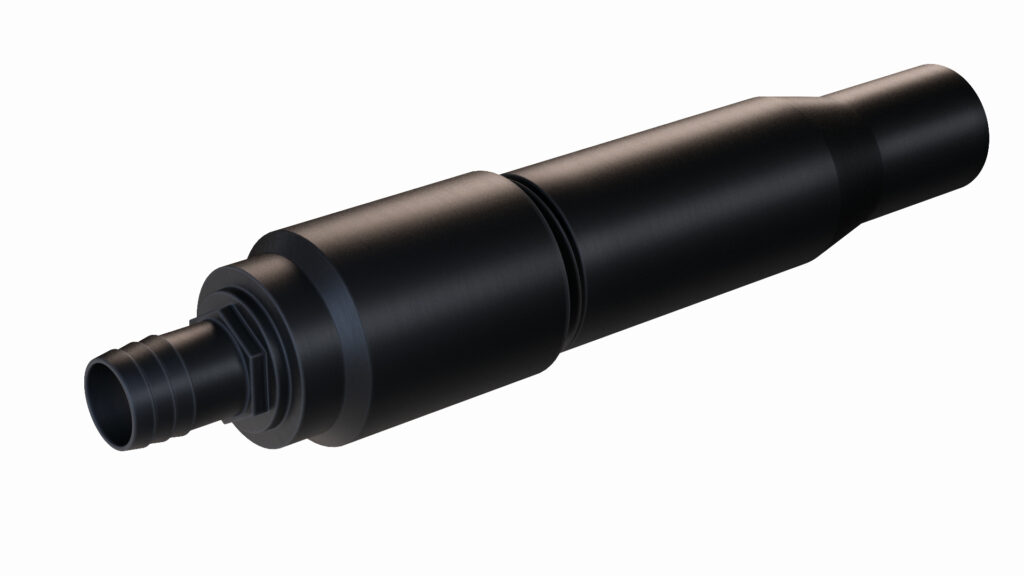
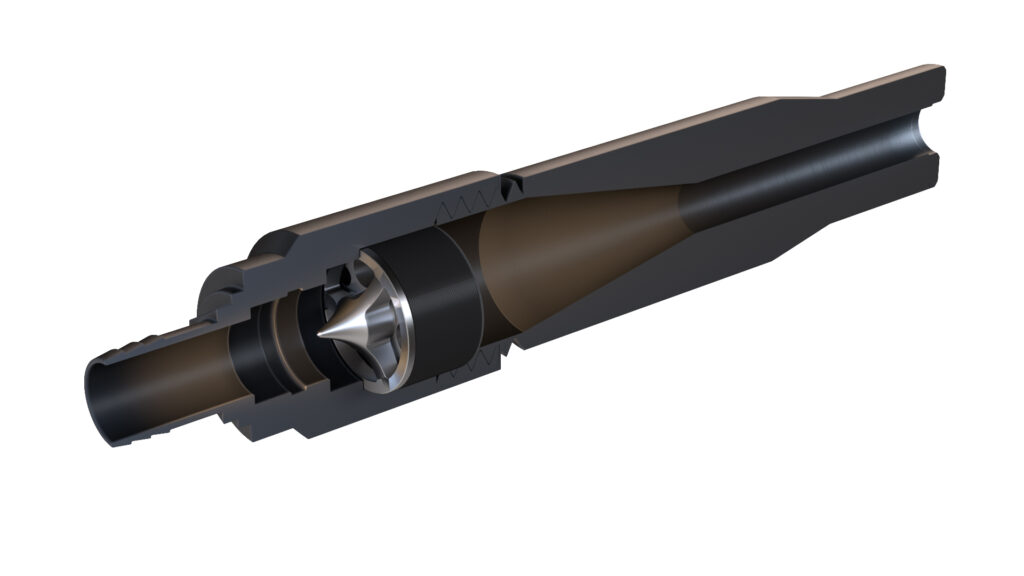
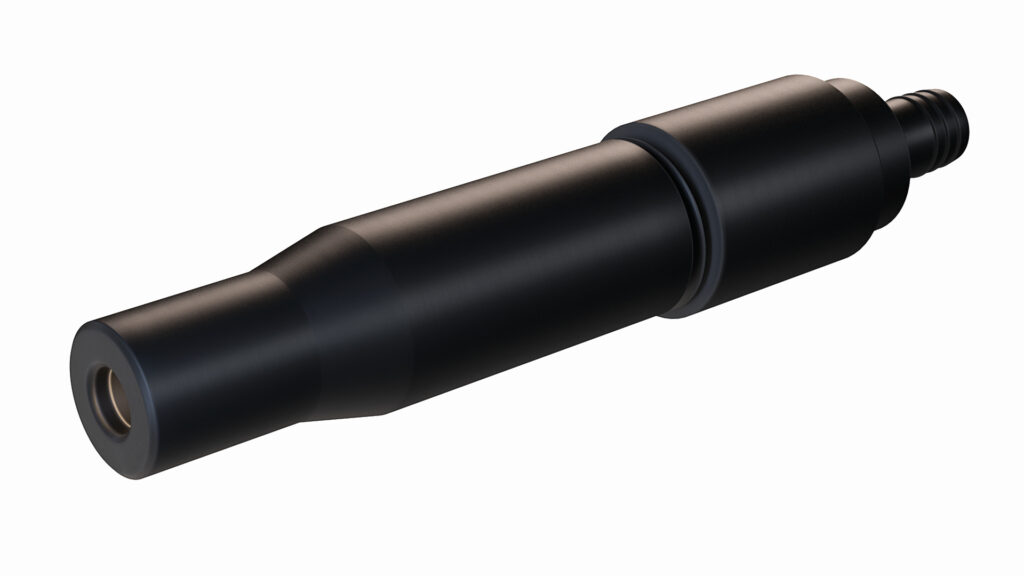
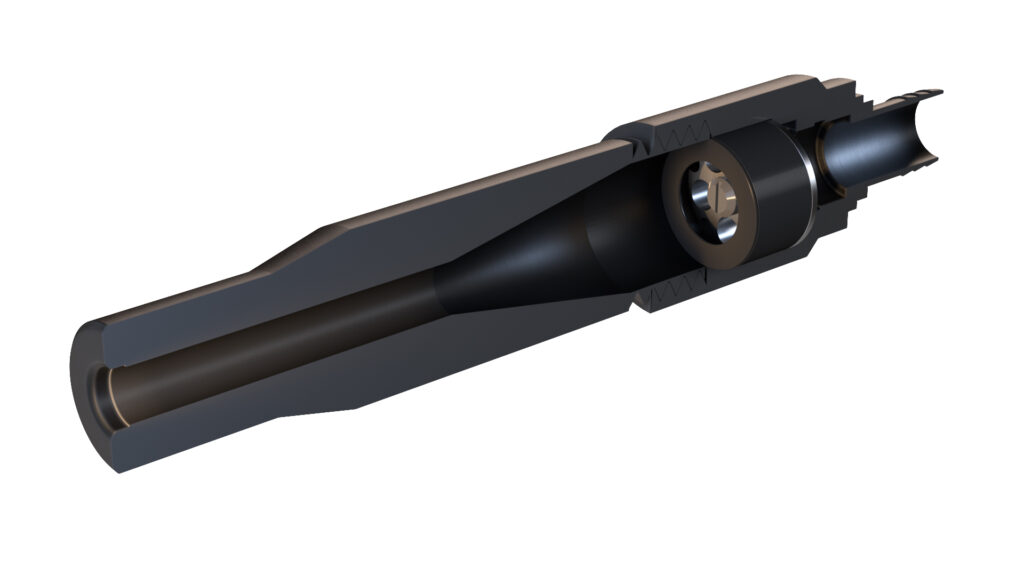
Stainless steel glass-bead blasting: good results always the first time round
With the ROTIN® 3, the rotating insert
Glass-bead blast a large stainless-steel surface, and get it right first time round? From now on, everyone can thanks to the ROTIN®. This innovative tool fits into the jet nozzle, and widens the jet. It eliminates problems with edges, patches or streaks on stainless-steel surfaces, and the roughness complies with the EHEDG standard.
Use the ROTIN® to make your stainless-steel products suitable for the food industry, pharmaceutical sector, or any other company that needs beautiful, smooth results.
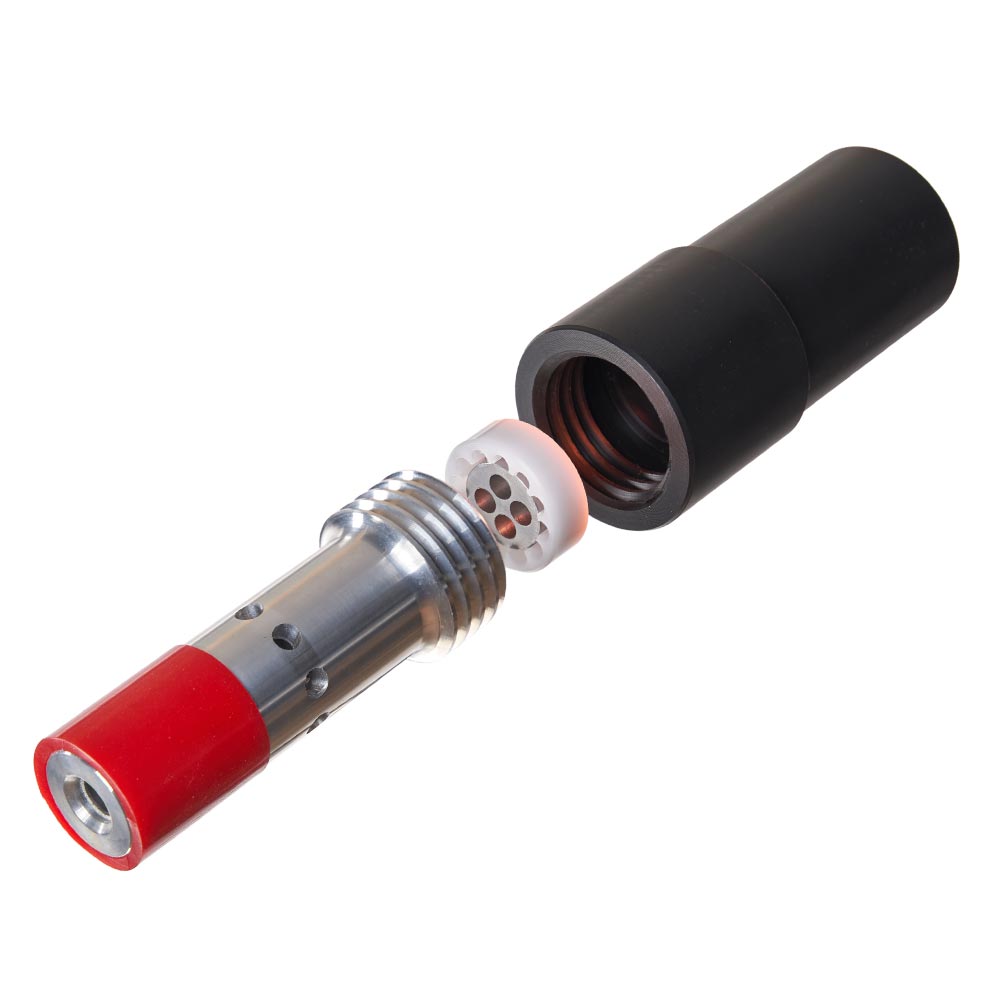
View the result
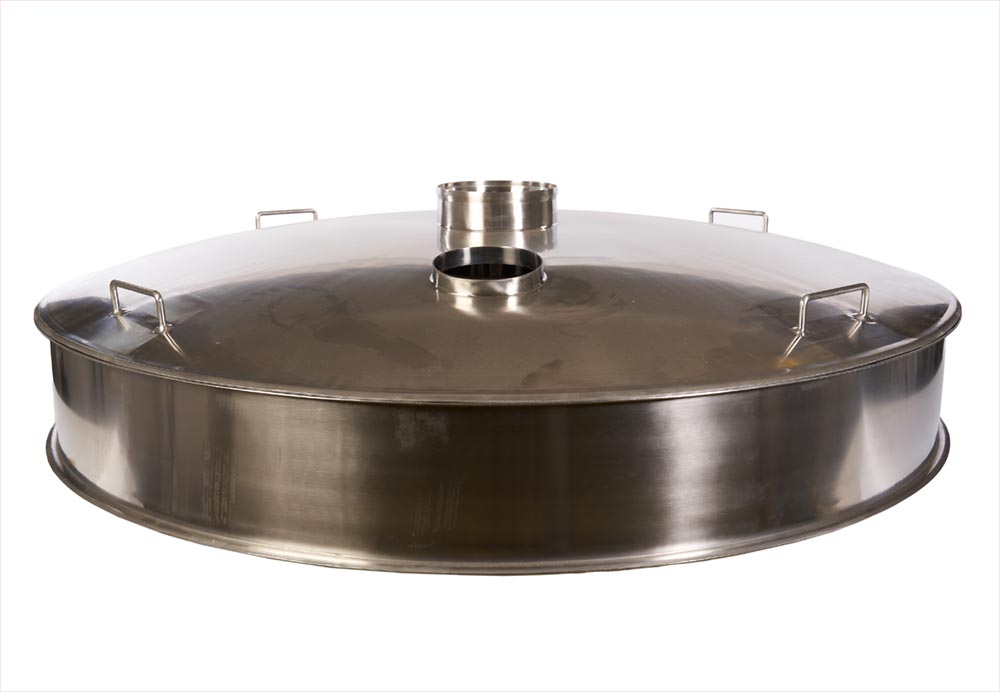
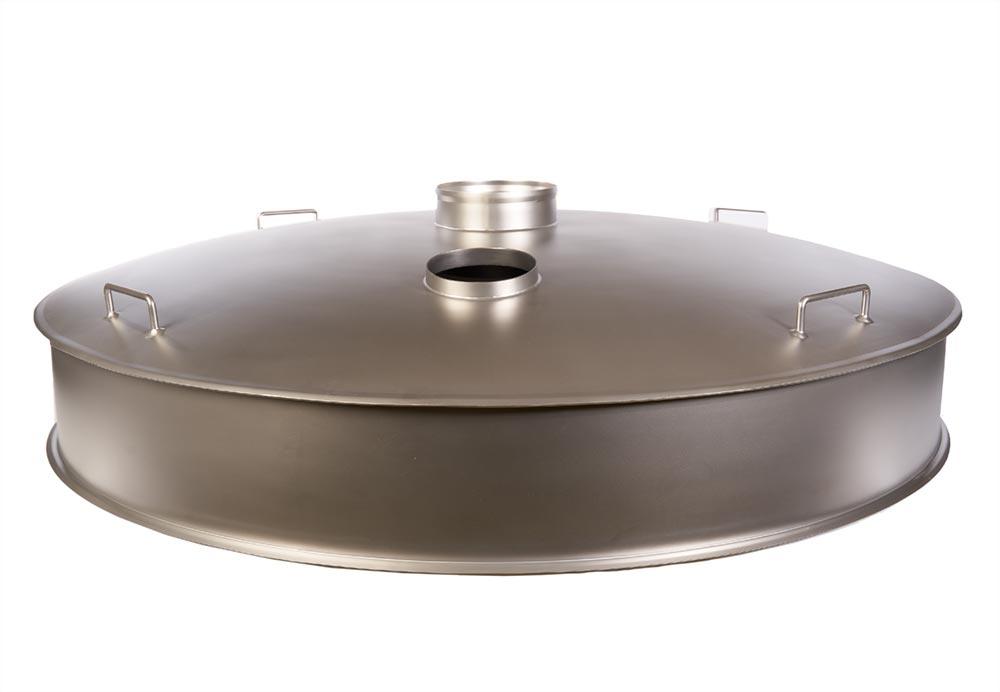
Made in Holland, quality guaranteed
The ROTIN® is produced in the Netherlands, and carefully inspected by Kalfsvel Coating, so excellent, consistent quality is standard. That’s a guarantee.
Rotin on Tour
PaintExpo takes place biennially in Karlsruhe as a showcase for innovations, applications, future technologies, and trends related to all aspects of industrial coating.
The fair encompasses the entire range of international products and services in the supply chain for industrial coating technology.
The broad spectrum of products extends from spray guns, equipment, and materials to automation technology.
Rotin was present here together with Airblast, the global distributor of Rotin.
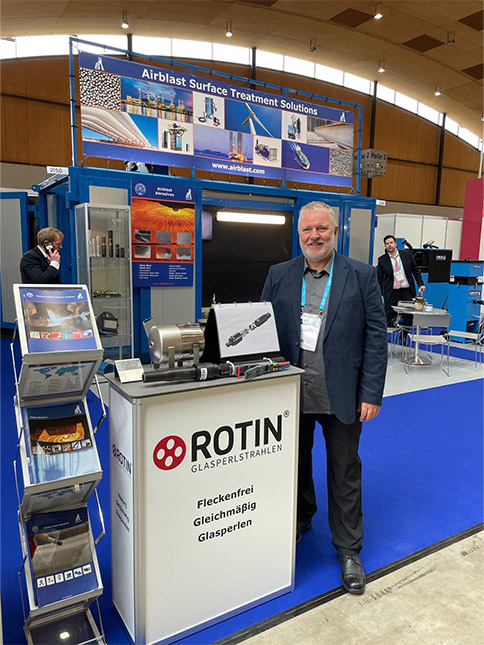
Benefits for suppliers and customers
Stainless-steel blasting with the ROTIN® offers benefits to both machining companies and customers. The desired result is achieved more quickly, and the customer is assured of a smooth, finished product which bacteria and viruses are unable to cling to, and which can be properly cleaned.
How glass bead-blasting with the ROTIN® 3 works
Glass-bead blasting is used to make stainless-steel surfaces smoother and more even visually. The surface is blasted, reducing peaks and opening valleys without cavities (openings) at the micro level. A very fine surface profile is created, where dirt can only form deposits on the peaks. The adhesive strength is minimal, so that the surface remains cleaner and can be cleaned better.
ROTIN® is also used to glass-bead blast stainless-steel surfaces, but gives a better, faster and more attractive result due to the unique way it works. This rotating insert (ROTIN) is placed in the blast nozzle. This insert widens the jet proportionally, and sprays it at an oblique angle. Because the jet widens equally, it blasts every surface with equal intensity at every angle. The blasting is done at a lower pressure, 3 bar instead of 6 bar, and uses 40/70 glass beads instead of 100/200 beads.
Re-blasting or reworking is no longer necessary thanks to the wider, oblique jet. The surface is blasted neatly and smoothly first time round, with no patches and a finer surface profile than that achieved with standard glass-bead blasting.
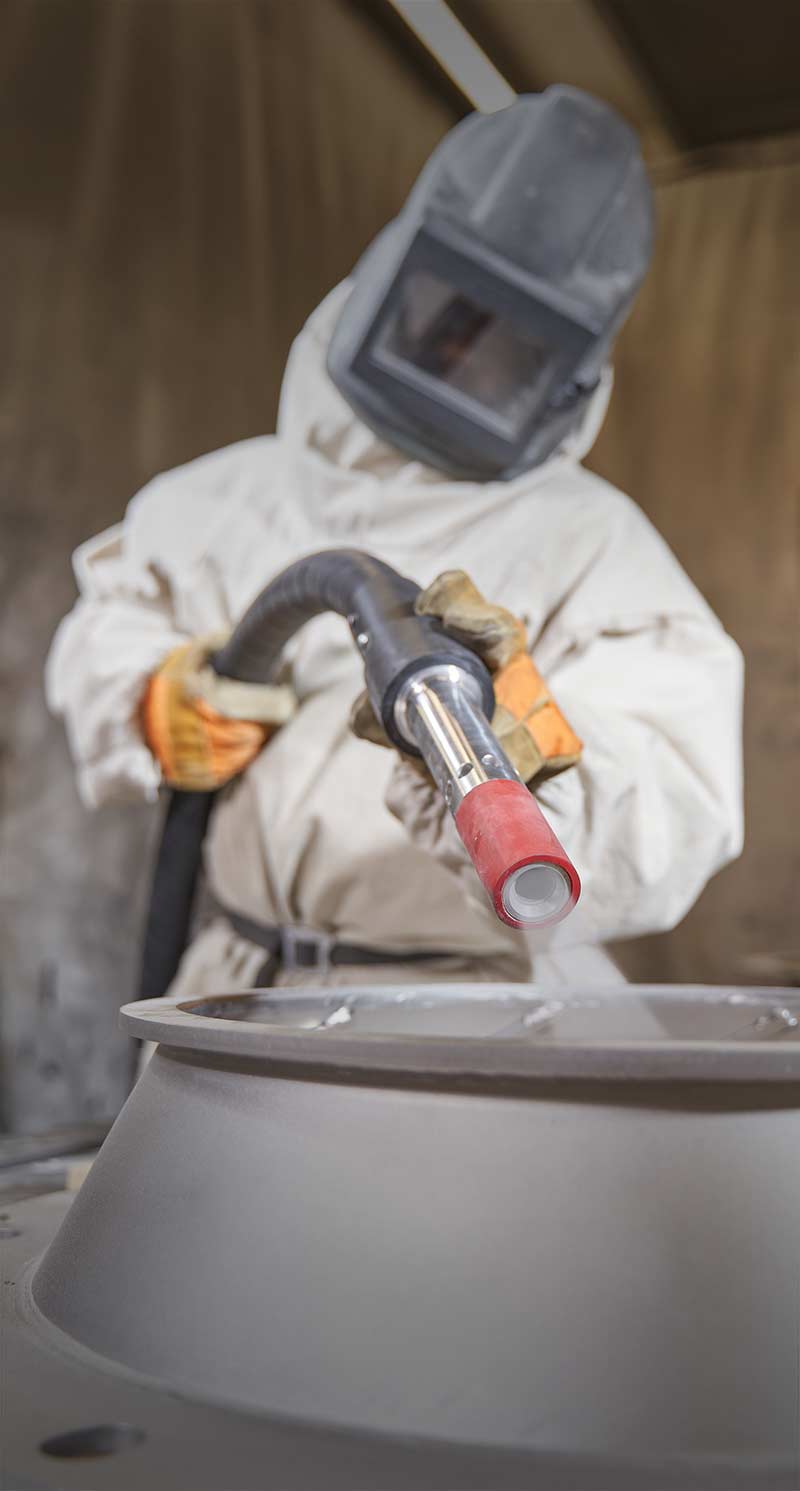
Excellent, smooth blasting results at every angle every time
Glass-bead blasting on stainless steel with the ROTIN® always gives good results,
because it blasts with a wide, uniform rotating jet at an oblique angle. This means the result is always smooth, irrespective of who does the blasting and from which angle you look at it.
Excellent, smooth blasting results at every angle every time
Glass-bead blasting on stainless steel with the ROTIN® always gives good results,
because it blasts with a wide, uniform rotating jet at an oblique angle. This means the result is always smooth, irrespective of who does the blasting and from which angle you look at it.
ROTIN® 3 in numbers
ROTIN® achieves a lot, with less:
- Energie: 3 bar i.p.v. 6 bar
- Glass beads: 40/70 instead of 100/200
- Ra-waarde: 0,2 – 0,6 instead of > 8,0
- Treatments: Good results first time round, instead of lots of reworking and problems.
- Lifespan: Unlimited, compared to about 10 years with stainless-steel coating
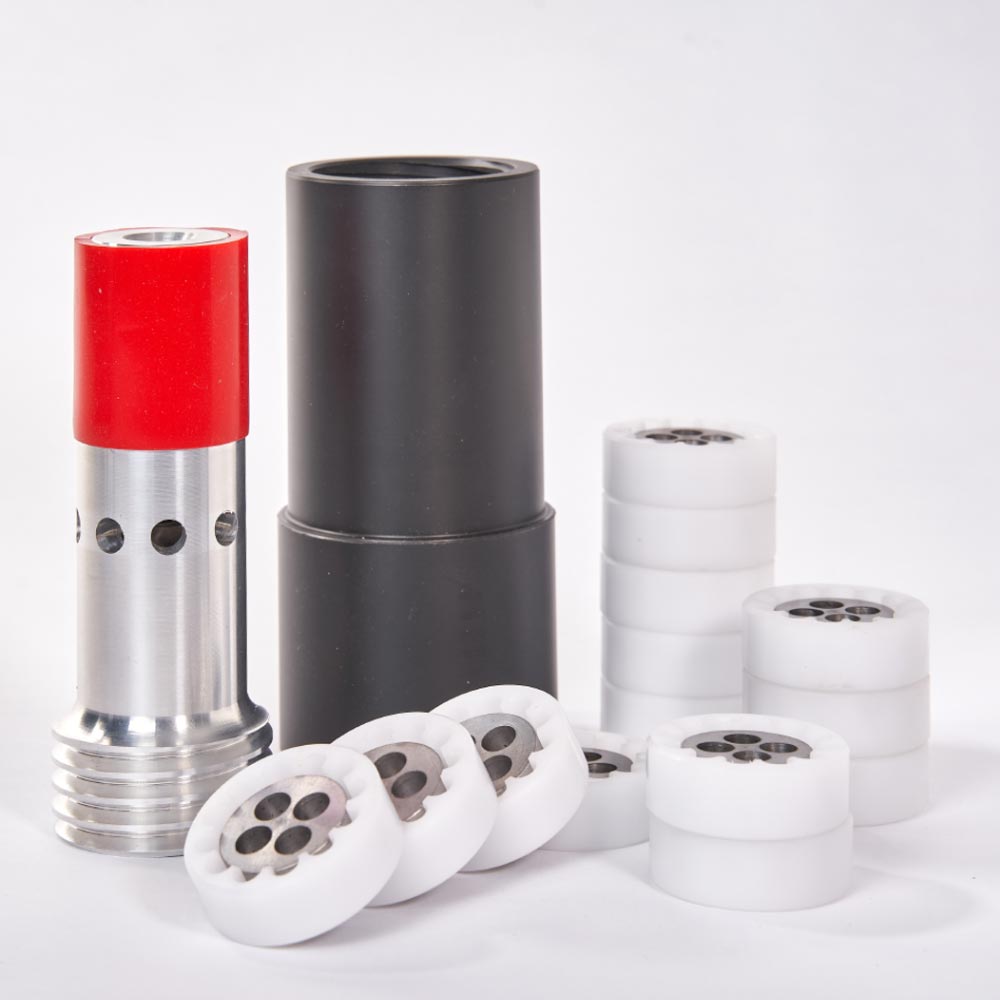
Stainless-steel blasting; a comparison of the methods
Stainless steel is glass-bead blasted to make the material sleek and smooth, eliminate weld discolouration and oxidation, and create an attractive, even surface with the desired roughness. We’ve drawn up a list of the various methods
available, and their pros and cons:

ROTIN® 3 for the food industry and pharmaceutical sector
Material glass-bead blasted with the ROTIN® meets the strict EHEDG standard, the stainless-steel food grade norm with Ra < 0.8 as a guideline. It’s therefore suitable for manufacturing equipment in the food industry and pharmaceutical sector.
The surface roughness (Ra) of a stainless-steel surface blasted with the ROTIN® at 3 bar using 40/70 glass beads is 0.2 to 0.6 microns. This Ra means that any cavities in the surface are so small that dirt and bacteria can no longer settle there. At the same time, the surface still contains enough cavities to reduce the adhesive force and allow the surface to be cleaned properly.
ROTIN® 3 for metal-coating companies
Standard glass-bead blasting uses a straight, narrow jet, which requires craftsmanship and experience. Someone with these professional skills is not always available, so glass-bead blasting can be a labour-intensive process at many metal-coating companies. After checking under daylight, the blasted product often has to be reworked. This takes more time and energy, and the resulting product often still shows patches and streaks. In addition, ordinary 100/200 glass beads at 6 bar result in a coarser surface (< 8 micron).
With the ROTIN®, every metal-coating company can obtain good glass-bead blasting results on stainless steel. The end product looks sleek and smooth, has a lower Ra value, and the work can be completed in less time with less experienced blasting operators.
The ROTIN® 3, a revolutionary invention
from metal-coating company Kalfsvel
Cees Kalfsvel at Metaalcoating Kalfsvel in Zaandam (NL) is a coating specialist. He noticed that experienced workers achieved the best results with glass beads, but those without such experience could never get the desired smooth, streak-free surface so quickly. As a result, he started looking for a better and easier method of glass-bead blasting that would also obtain the surface roughness required by the food and pharmaceutical industries.
Lots of prototypes were designed and tested, but each one was rejected by employees. The project was put on ice, but Cees wanted to try one more idea. He designed the insert with slightly angled holes and extra spaces in the surrounding ring, so that it would rotate without seizing, and then asked an employee to give it a try. It was a success!
Designed by practical experience, the ROTIN® has turned out to be a revolutionary invention that is now used as standard at Kalfsvel Coating, as well as increasingly more other coating companies. The same result is achieved everywhere; once the ROTIN® has been tried, nobody wants to go back to the old method. The reason is that it gives great results first time round, and always blasts neatly without leaving streaks. Exactly what the ROTIN® was designed to do.
Lots of prototypes were designed and tested, but each one was rejected by employees. The project was put on ice, but Cees wanted to try one more idea. He designed the insert with slightly angled holes and extra spaces in the surrounding ring, so that it would rotate without seizing, and then asked an employee to give it a try. It was a success!
Designed by practical experience, the ROTIN® has turned out to be a revolutionary invention that is now used as standard at Kalfsvel Coating, as well as increasingly more other coating companies. The same result is achieved everywhere; once the ROTIN® has been tried, nobody wants to go back to the old method. The reason is that it gives great results first time round, and always blasts neatly without leaving streaks. Exactly what the ROTIN® was designed to do.
ROTIN
ROTIN is subject to intellectual property rights, including patent, trademark, design and copyright, as well as know-how and trade secrets.
It is expressly forbidden to use these intellectual property rights without the written consent of the owner, Kalfsvel Materieel B.V. , unless Kalfsvel Materieel B.V. has given its express written consent.
ROTIN means the glass bead insertion produced and sold by Kalfsvel Materieel B.V. under the ROTIN brand, including related accessories, services and other materials, including – but not limited to – texts, illustrations, design, photos, manuals and websites.
The buyer and user of the ROTIN acknowledges these rights and shall refrain from any infringement thereof.
ROTIN official outlets and users
At www.rotin.nl you will find a list of official ROTIN outlets and officially authorized ROTIN users. Please contact us for listing your name on this list and the requirements for doing so.
Official point of sale
Airblast B.V. – Headquarters
Contact: Remon Ris
Tel: +31 72 571 8002
Users of ROTIN
Kalfsvel Coating
Tel: +31 75 617 4355